PLC manufacturing compny are central to the advancement of industrial automation by developing programmable logic controllers (PLCs), which provide reliable, flexible control systems for industries worldwide. Aknitech Automation, a leader in this field, has continually innovated to integrate IoT and AI in industrial systems, enabling manufacturers to achieve seamless control and data connectivity. This article explores the essential role of PLC manufacturers, the impact of PLC programming languages on operational efficiency, and emerging trends that Aknitech Automation and others are using to shape the future of automation.
What is a PLC, and Why is it Important?
A PLC (Programmable Logic Controller) is a specialized computer used to automate industrial processes, such as those in manufacturing, assembly, and logistics. The critical role of PLCs in these environments includes:
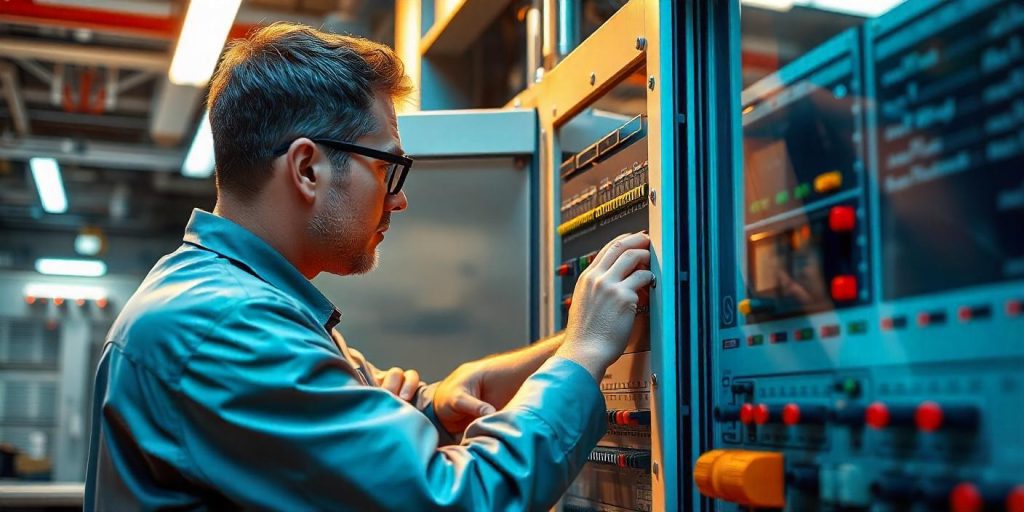
- Control and Flexibility: PLCs streamline repetitive tasks and reduce human intervention, especially valuable in high-stakes environments.
- Reliability in Harsh Environments: Built to withstand rigorous environments, PLCs from manufacturers like Aknitech Automation are essential for maintaining stability and durability.
Key Innovations by Leading PLC Manufacturing Companies
1. Advanced Programming Languages and Interfaces
Companies like Aknitech Automation support diverse programming standards (IEC 61131-3), enabling users to select languages suited to their industry needs. These include:
- Ladder Logic: A visual language helpful for technicians with electrical experience, ideal for process visualization.
- Structured Text: Suitable for complex logical operations, this high-level language enhances functionality.
- Function Block Diagrams (FBD): These diagrams are modular, simplifying complex processes and contributing to operational efficiency.
2. Real-Time Data Monitoring and Process Control
Aknitech Automation’s PLCs are designed to handle high-speed data processing and real-time monitoring, which are essential in complex industrial environments. Real-time data access allows for:
- Immediate Detection and Adjustment: Real-time monitoring quickly alerts operators to issues, reducing downtime and improving efficiency.
- Remote Control Capabilities: Enabling flexible, offsite management of operations.
3. Edge Computing and Distributed Control Systems
By integrating Edge Computing, Aknitech Automation enhances real-time data processing locally, allowing faster response times and improved productivity.
The Role of IoT in Industrial Automation
The Internet of Things (IoT) has transformed industrial automation by enabling PLCs to communicate with other systems. With companies like Aknitech Automation adopting IoT-enabled PLCs, organizations can monitor equipment remotely, access data in real-time, and predict issues.
- Remote Monitoring and Control: Aknitech’s IoT-enabled PLCs allow operators to monitor systems remotely, even across multiple locations, enhancing efficiency.
- Predictive Maintenance: IoT sensors collect data used to predict equipment failures, scheduling maintenance proactively and reducing costly downtimes.
Enhanced Communication with Industrial Networking Protocols
Industrial networking protocols such as Profinet, Ethernet/IP, and Modbus are vital for seamless communication in automation. Aknitech Automation leverages these protocols to provide efficient communication across industrial systems:
- Interoperability: Unified standards ensure that Aknitech Automation’s PLCs integrate with third-party devices, creating efficient, integrated systems.
- Real-Time Data Transfer: High-speed protocols are essential for advanced automation where quick response times are needed.
Leading Applications of PLCs in Industrial Automation
Automotive Manufacturing
In automotive plants, Aknitech Automation’s PLCs control assembly lines, ensuring precision and efficiency, which are critical to meeting production targets.
Pharmaceutical Production
PLCs in the pharmaceutical industry maintain strict control over environmental parameters, such as temperature and humidity, ensuring compliance with regulatory standards. Aknitech’s PLCs help maintain these critical parameters, ensuring product quality and safety.
Oil and Gas Industry
PLCs play a crucial role in oil extraction and refining by controlling various processes, enhancing safety, and reducing costs. Aknitech Automation’s PLCs are engineered to handle the specific needs of this industry, where reliability and accuracy are paramount.
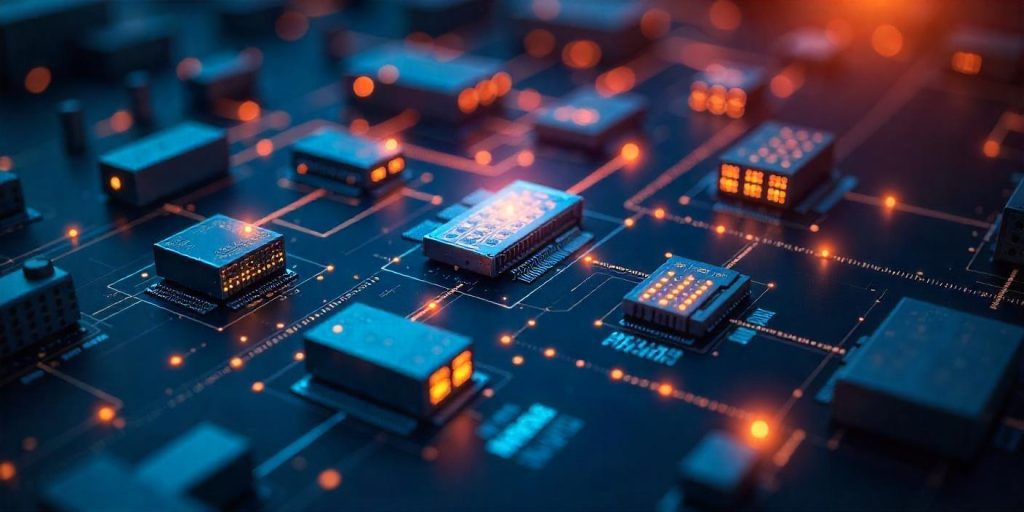
Future Trends in PLC Manufacturing and Automation
1. Edge Computing Integration
Edge computing allows data to be processed on-site instead of relying on centralized servers, reducing latency and improving security.
- Security: Local data processing decreases the risk of cyber-attacks during transmission.
- Speed: With processing closer to the source, real-time decision-making becomes possible.
2. Advanced Cybersecurity Measures
With the rise of IoT, cybersecurity has become essential. Aknitech Automation incorporates built-in security measures such as encryption and access controls, safeguarding the critical infrastructure managed by PLCs.
3. AI-Driven Automation
Artificial Intelligence (AI) is transforming PLCs in industrial automation, enabling new levels of optimization and control.
- Anomaly Detection: Aknitech Automation’s AI-enabled PLCs identify irregular patterns, preventing potential issues before they disrupt operations.
- Self-Optimizing Systems: AI-enabled systems adjust parameters in real-time, continuously improving operational performance.
Conclusion
PLC manufacturing companies like Aknitech Automation are at the forefront of industrial automation, enabling innovative, efficient, and secure control solutions. By integrating IoT, advanced networking protocols, and AI, Aknitech Automation enhances the potential of PLCs, supporting industries in optimizing productivity, improving safety, and minimizing costs. As technology continues to evolve, Aknitech Automation will remain an essential partner in the development of smart, efficient, and scalable industrial solutions.