Manufacturing is evolving rapidly, and industries are shifting towards automation and digitization to enhance efficiency, productivity, and quality. A smart factory represents the next step in this transformation by integrating connected systems, real-time data analytics, and automation technologies to optimize production processes. These factories rely on interconnected machinery, sensors, artificial intelligence, and cloud computing to operate with minimal human intervention.
Aknitech Automation specializes in implementing advanced automation solutions that help businesses transition to smart factory environments. By adopting intelligent manufacturing technologies, industries can enhance operational efficiency, reduce downtime, and improve product quality.
This blog explores the concept of a smart factory, its key features, technologies driving the transformation, and the impact on modern manufacturing.
Understanding a Smart Factory
A smart factory is a highly digitized and automated production facility where physical processes are connected through IoT, AI, machine learning, and cloud computing. Unlike traditional manufacturing units that rely on manual supervision, smart factories use real-time data collection and analytics to make autonomous decisions, optimize workflows, and enhance production quality.
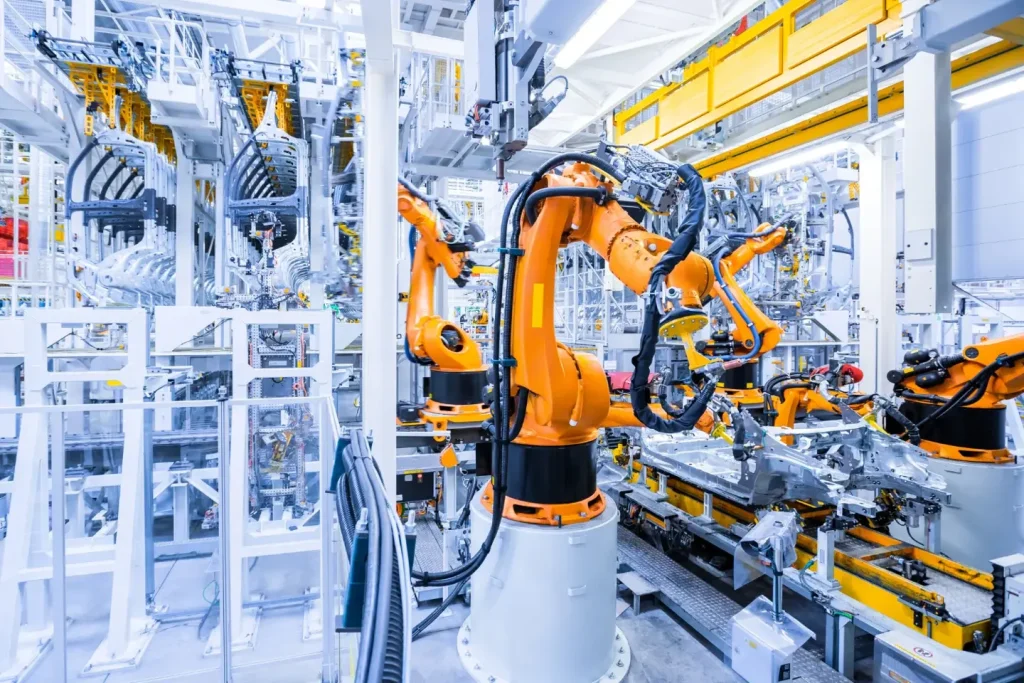
A smart factory operates through:
- Connected sensors and IoT devices that gather real-time data
- AI-driven analytics that predict equipment failures and optimize production
- Automated robotic systems that handle repetitive tasks with precision
- Cloud-based platforms that enable remote monitoring and decision-making
- Cybersecurity systems that protect manufacturing data and networks
These advanced capabilities enable industries to maintain high efficiency, reduce waste, and adapt to changing market demands.
Key Technologies Driving the Smart Factory Revolution
1. IoT and Connected Devices
IoT enables communication between machines, equipment, and operators in real-time. Sensors collect data on temperature, pressure, energy consumption, and machine performance, allowing for predictive maintenance and improved decision-making.
2. Artificial Intelligence and Machine Learning
AI analyzes production data, identifies patterns, and predicts potential equipment failures before they occur. Machine learning models help optimize production schedules, improve product quality, and reduce operational risks.
3. Robotics and Automation
Smart factories integrate industrial robots that perform repetitive tasks with precision. These robots work alongside human operators, increasing efficiency while reducing labor costs. Automated assembly lines, robotic arms, and AI-powered quality control systems enhance production speed and accuracy.
4. Cloud Computing and Edge Computing
Cloud computing allows manufacturers to store and process vast amounts of production data remotely, enabling real-time monitoring and control. Edge computing reduces latency by processing critical data closer to the production floor, ensuring faster decision-making.
5. Digital Twin Technology
A digital twin is a virtual model of a physical manufacturing process or equipment. It enables manufacturers to simulate and test production processes in a digital environment before applying changes to the actual factory floor. This reduces the risk of production errors and enhances operational efficiency.
6. Cybersecurity and Data Protection
As factories become more connected, they become vulnerable to cyber threats. Smart factories implement advanced cybersecurity protocols, such as encryption, access control, and network segmentation, to protect sensitive data and prevent unauthorized access.
How a Smart Factory is Changing Modern Manufacturing
1. Enhanced Efficiency and Productivity
By automating routine tasks and utilizing real-time data analytics, smart factories optimize production processes, minimize downtime, and increase overall efficiency. Machines adjust operations dynamically based on current demand, ensuring optimal resource utilization.
2. Predictive Maintenance for Reduced Downtime
Traditional factories follow scheduled maintenance routines, often leading to unnecessary repairs or unexpected failures. In a smart factory, predictive maintenance ensures that machines are serviced only when needed, preventing breakdowns and reducing maintenance costs.
3. Improved Product Quality and Reduced Waste
Advanced analytics and automated quality control systems detect defects early in the production cycle, reducing material waste and ensuring higher product quality. AI-powered inspection systems improve consistency and minimize errors.
4. Greater Flexibility and Customization
Smart factories enable manufacturers to produce customized products efficiently by adjusting production lines automatically. Real-time monitoring allows for quick adaptation to changing consumer demands without slowing down production.
5. Sustainability and Energy Efficiency
Energy consumption in manufacturing is a significant operational cost. Smart factories use IoT-driven energy management systems to track power usage and optimize energy consumption, reducing costs and environmental impact.
6. Seamless Supply Chain Integration
Smart factories are connected to digital supply chain networks that enable real-time tracking of raw materials, inventory levels, and logistics. This improves coordination with suppliers and reduces delays in production.
Industries Benefiting from Smart Factory Solutions
Automotive Manufacturing
Smart factories optimize vehicle assembly lines using robotics, AI-driven quality control, and predictive maintenance to enhance production speed and reduce defects.
Electronics and Semiconductor Industry
High-precision manufacturing requires real-time monitoring and automation. Smart factories in the electronics sector improve product testing, minimize waste, and increase efficiency.
Pharmaceutical and Healthcare Manufacturing
Strict quality and regulatory standards in pharmaceuticals demand precise monitoring. Smart factories use AI and IoT to ensure compliance, automate drug manufacturing, and maintain sterile environments.
Food and Beverage Industry
Automated processing lines, IoT-enabled refrigeration monitoring, and AI-driven quality control systems enhance food safety and production efficiency.
Textile and Apparel Industry
Smart factories use automated sewing machines, real-time quality inspection, and digital design technologies to increase customization and reduce material waste.
How Aknitech Automation is Transforming Manufacturing
Aknitech Automation provides advanced smart factory solutions tailored to industry-specific needs. Their expertise includes:
- Implementing IoT-driven real-time monitoring systems
- Integrating AI-powered predictive maintenance solutions
- Deploying robotics and automation for improved efficiency
- Optimizing energy consumption with smart management systems
- Enhancing cybersecurity for connected manufacturing networks
By adopting smart factory solutions, businesses can improve operational efficiency, reduce costs, and stay competitive in the rapidly evolving manufacturing landscape.
Conclusion
A smart factory represents the future of manufacturing, where automation, data-driven decision-making, and interconnected systems enhance productivity and efficiency. By integrating IoT, AI, cloud computing, and robotics, industries can optimize production, reduce downtime, and improve product quality.
Aknitech Automation offers cutting-edge smart factory solutions that help businesses transition to intelligent manufacturing environments. As industries continue to evolve, embracing automation and digital transformation will be essential for staying ahead in the competitive market.