PLC-based electrical panels are an integral part of industrial automation systems, helping to streamline processes and ensure smooth operation. Maintaining and upgrading these panels is essential for ensuring long-term reliability, efficiency, and safety in industrial environments. Whether you’re dealing with complex automation systems or smaller installations, taking care of the Programmable Logic Controller (PLC) panels can save you time and money by avoiding unexpected downtime.
In this blog, we’ll explore PLC panel maintenance, ways to upgrade PLC panels, and provide valuable insights into PLC system enhancements to keep your operations running efficiently.
1. Understanding PLC-Based Electrical Panels
PLC-based electrical panels are control units that manage machinery, equipment, and processes in industries. They consist of various components like the PLC itself, circuit breakers, relays, power supplies, and input/output modules that connect to different parts of the machinery. Proper functioning of the PLC panel is crucial as any failure or inefficiency in the system can lead to costly downtimes and disruptions in production.
Maintaining and upgrading these panels can prolong their life, improve productivity, and ensure the safety of the working environment.
2. Why Is Regular PLC Panel Maintenance Important?
Regular PLC panel maintenance is essential to avoid malfunctioning, reduce breakdown risks, and ensure smooth operations. Many companies overlook the importance of preventive maintenance, focusing only on fixing problems once they occur. However, consistent upkeep helps you detect potential issues before they become major problems.
Here are key benefits of PLC panel maintenance:
- Minimizing downtime: Regular inspection and maintenance help in identifying minor issues that can prevent complete system failure.
- Improving efficiency: Well-maintained PLC panels contribute to better system performance and efficiency, reducing energy consumption.
- Enhancing safety: Electrical panels house high-voltage equipment, and maintaining them ensures the safety of the operators.
- Prolonging equipment life: Preventive maintenance extends the life of PLC components, minimizing the need for expensive replacements.
- Reducing repair costs: Early detection of issues reduces the cost of major repairs and replacements.
3. Essential Steps for PLC Panel Maintenance
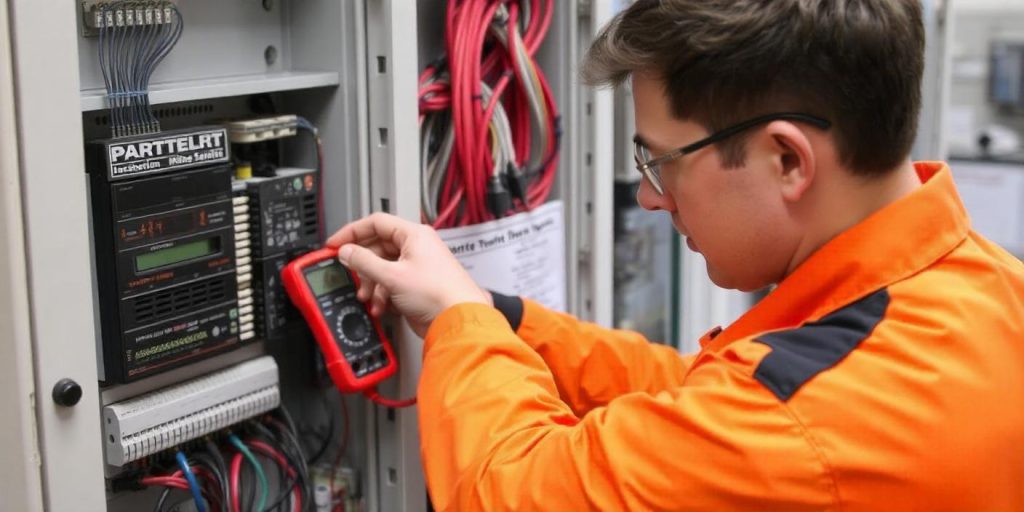
To ensure optimal performance, follow these steps to maintain PLC-based electrical panels:
A. Regular Inspection
Conduct regular visual and physical inspections to check for signs of wear, corrosion, overheating, or loose wiring. Inspect connections to ensure they are secure and intact, as loose wires can cause intermittent issues in the control system.
- Check for dust accumulation in the panel and clean it if necessary, as dust can cause overheating and electrical shorts.
- Make sure that the panel’s ventilation is not blocked, allowing adequate airflow to prevent overheating.
B. Testing and Diagnostics
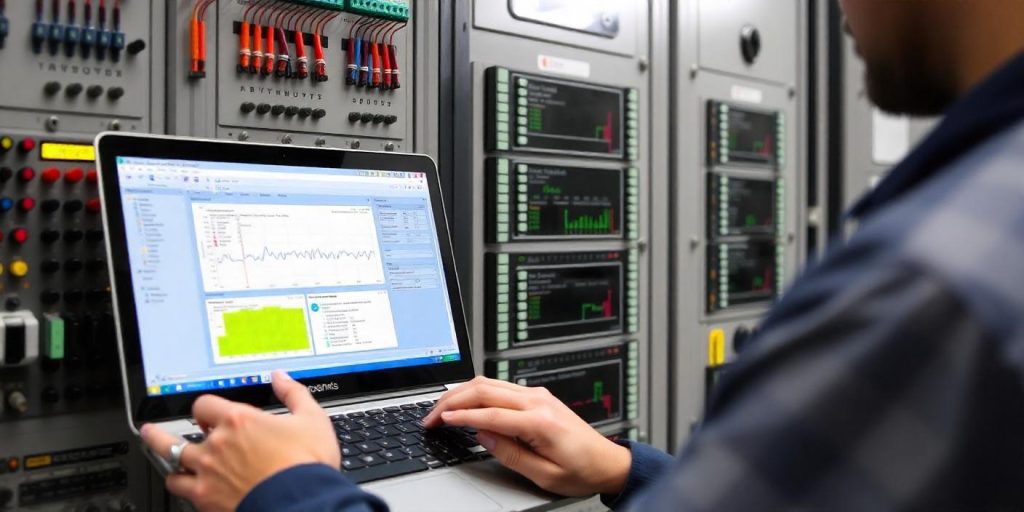
Run diagnostic checks to ensure that all the PLC components are functioning correctly. Modern PLC systems come with built-in diagnostic tools that help you assess the health of the system. Utilize these diagnostics to identify any underlying issues in the power supply, input/output modules, or communication networks.
- Conduct voltage and current tests to verify the power supply to all components.
- Test the emergency stop buttons and any other safety-related devices regularly to ensure they function as intended.
C. Updating Software and Firmware
PLC manufacturers release regular updates for their software and firmware to improve functionality, fix bugs, and enhance security. Keeping the software up to date is essential for PLC system enhancements and maintaining operational efficiency.
- Schedule periodic updates to the PLC software and firmware.
- Make sure that backups of current configurations are available before performing any updates to avoid data loss.
D. Calibration and Tuning
Periodic calibration and tuning of the sensors and instruments connected to the PLC system are critical for accurate data collection and processing. Over time, sensors can drift, causing inaccurate readings, which may affect the overall system performance.
- Perform regular calibration of sensors to ensure precise measurements.
- Fine-tune the system for optimal performance and to avoid unnecessary strain on the components.
E. Documentation
Ensure that all changes, maintenance activities, and upgrades are well-documented. Having detailed records helps during troubleshooting and keeps track of the PLC panel’s maintenance history. Proper documentation also ensures that your team remains informed about any changes or updates made to the system.
4. Upgrading PLC Panels for Enhanced Performance
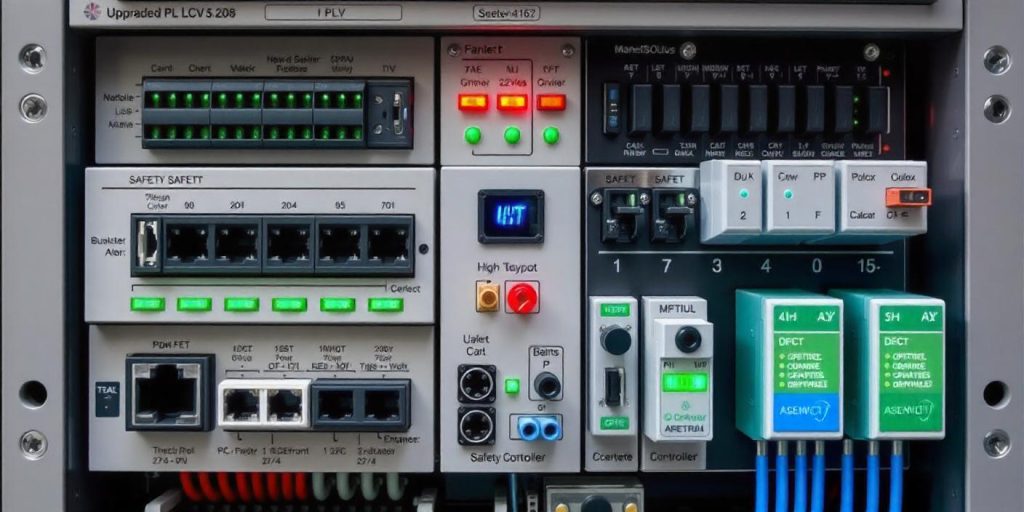
In addition to regular maintenance, upgrading PLC panels is sometimes necessary to meet the growing demands of industrial automation. Upgrading not only helps enhance system efficiency but also provides access to new features and improved performance.
Here are key considerations when upgrading your PLC-based electrical panels:
A. Assessing the Need for an Upgrade
Determine whether the PLC panel needs an upgrade by evaluating the current performance, technology, and future scalability. If you experience frequent malfunctions, outdated technology, or limitations in the current system, it may be time to consider upgrading.
- Assess the processing speed and memory capacity of the existing PLC to determine if it can handle new automation tasks.
- Evaluate the input/output (I/O) modules and communication protocols for compatibility with newer equipment.
B. Implementing Modern Communication Protocols
Upgrading the communication protocols of your PLC panel can significantly enhance its performance. Modern communication standards such as Ethernet/IP, Profinet, or Modbus TCP offer faster data transfer rates and better integration with other systems.
- Install new communication modules to facilitate real-time data exchange and seamless integration with the factory’s central control system.
- Ensure that your system is capable of handling the Industrial Internet of Things (IIoT) for future expansions.
C. Increasing Processing Power
If your current PLC struggles to manage the increased demands of your automation system, consider upgrading to a more powerful controller. Modern PLCs offer better processing capabilities and faster response times, ensuring smoother operations and quicker troubleshooting.
- Choose PLCs with enhanced processing power to manage complex automation tasks.
- Upgrade the memory capacity to store more complex programs.
D. Enhancing Safety Features
Modern safety standards demand higher levels of protection for machinery and personnel. Upgrading your PLC panel with advanced safety features like fail-safe I/O modules, enhanced diagnostic capabilities, and emergency stop systems can ensure greater safety.
- Implement advanced safety protocols such as Safety PLCs or dual-channel emergency stop circuits to improve overall safety.
- Regularly review and upgrade the safety components in line with regulatory standards.
E. System Redundancy
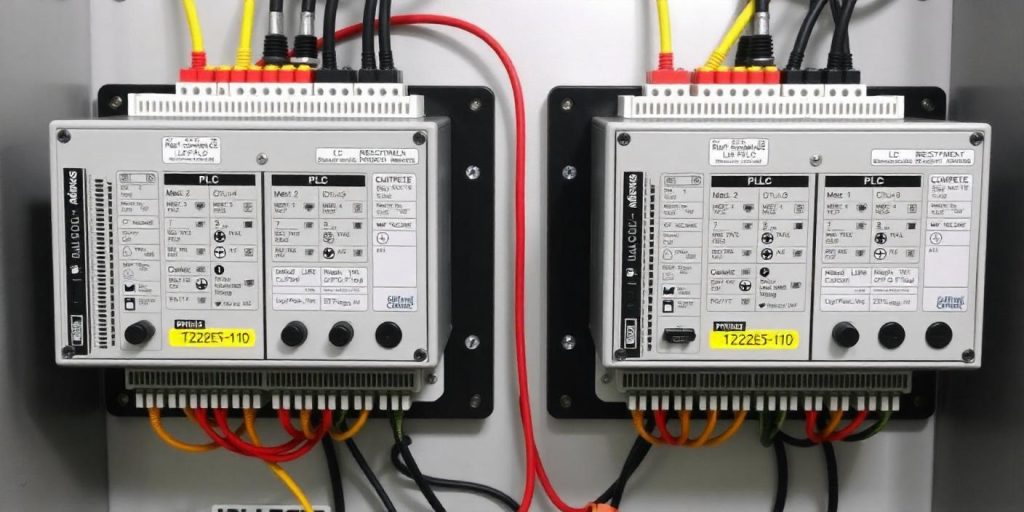
For industries where downtime is costly, system redundancy is crucial. Upgrading your PLC system to include redundant processors or power supplies ensures that operations continue even if one component fails.
- Consider implementing redundant PLC controllers and power supplies to prevent any single point of failure.
- Design a backup strategy that ensures continued operation during system malfunctions.
5. Best Practices for Panel Upkeep and System Enhancements
To keep your PLC-based electrical panels running efficiently, implement the following best practices:
- Training and Skill Development: Ensure that your team is well-trained in maintaining and upgrading PLC systems. Understanding the latest technology trends can help in quicker troubleshooting and efficient upgrades.
- Energy Efficiency: Regular maintenance and upgrading of PLC systems can improve energy efficiency, reducing overall operational costs.
- Collaborate with Experts: Partnering with companies that specialize in PLC panel maintenance and upgrades, like Aknitech Automation, ensures that your systems are always up to date and operating at peak efficiency.
Conclusion
Maintaining and upgrading PLC-based electrical panels is essential to ensure reliability, safety, and performance in any industrial setting. Regular maintenance reduces downtime and extends the life of your equipment, while upgrading to newer technologies enhances efficiency and prepares your systems for the future. By following the steps and best practices outlined above, you can ensure that your PLC panels continue to serve your automation needs effectively.
For expert help in maintaining or upgrading your PLC panels, Aknitech Automation provides specialized services designed to enhance system performance, improve efficiency, and keep your automation processes running smoothly.